ITT Bornemann & Blaser Swisslube –
Co-operation increases productivity and process security
International company ITT Bornemann tailors its high-tech pump systems to satisfy individual customer requirements. The pumps produced by the innovative company are primarily used in the oil and gas industry, as well as in the food, chemical and pharmaceutical sectors. The broad diversity in production means that the demands placed on coolants are also very high. The company managed to increase coolant sump life eightfold in co-operation with Blaser Swisslube by using B-Cool 9665. Machine cleanliness, human compatibility and consumption have all been optimized.
The Bornemann Locksmith’s store company was founded no less than 170 years ago, in 1853. Headquartered in Obernkirchen near Hanover, ITT Bornemann is now an internationally active manufacturer of high-tech pump systems. The company employs 250 people and has been part of the ITT Group since 2012, with its parent company located in the US.
Bornemann has been delivering continuous innovation to market in the pump segment for a whole century. The twin-spindle screw pump with external bearing was patented in 1934. Three-spindle screw pumps and progressive cavity pumps followed in the 1960s. In the 1980s, Bornemann’s multiphase pumps tapped into previously unknown economic opportunities. Multiphase technology avoids the so-called “flaring” of gas during oil production, allowing the gas to be recovered and utilized. In the food sector, Bornemann has developed self-cleaning pumps that have no dead legs. The stainless-steel pumps transport food with care and meet the highest quality standards.
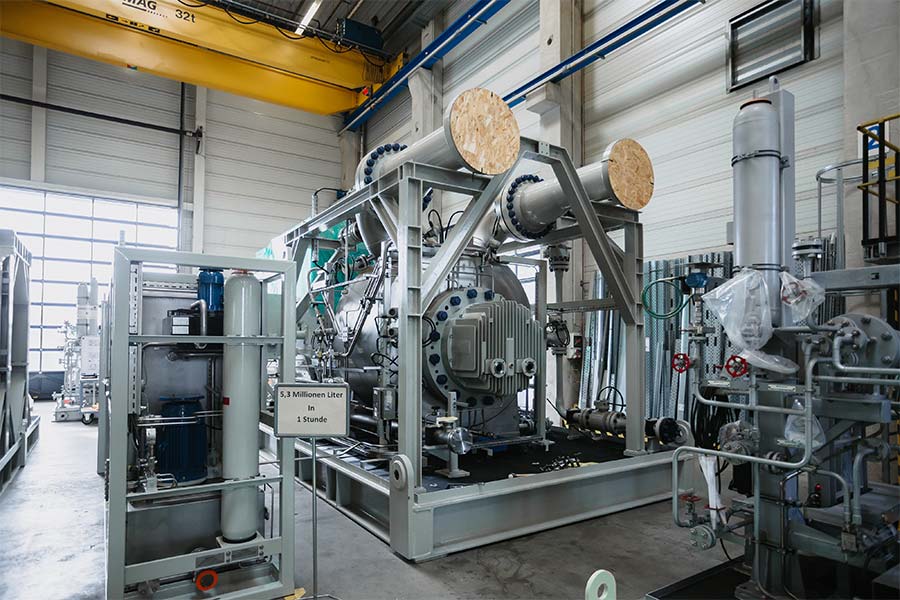
ITT Bornemann produces a wide variety of pumps. One of the larger models is currently being worked on.
High coolant demands
ITT Bornemann’s pumps are used in the oil and gas industry, as well as in the food, chemical and pharmaceutical sectors. Each year, around 2,500 pumps are produced and individually adapted to customer requirements. In particular, the gradient and conveying capacity are tailored to customer specifications in line with the particular application. Due to this very high level of variance, the production processes at ITT Bornemann are also very diverse. “We use a wide range of machine types. These include numerous turning machines for producing screw profiles, but also grinding and milling machines,” ITT Bornemann explains. “This means that the demands placed on the coolant are particularly stringent: We need a highly versatile product that works reliably and guarantees a high level of machine cleanliness.”
Executives from ITT Bornemann sought a meeting with the coolant experts from Blaser Swisslube in 2015. The coolant supplied by a competitor was a cause for concern: “The coolant was constantly spilling, forcing us to change it four times a year. As a result, the process stability was unsatisfactory and coolant consumption was too high,” recalled the experts from ITT Bornemann.
Following thorough on-site analysis, the Blaser specialists recommended B-Cool 9665. Carsten Liesegang, Application Engineer at Blaser Swisslube, explains: “B-Cool 9665 is a water-miscible, chlorine-free and semi-synthetic coolant with a low mineral oil content. The product is suitable for various machining processes and grinding tasks and is characterized by high cutting performance, low foaming, excellent corrosion protection, as well as very good rinsing and drainage properties. Finally, we expected B-Cool 9665 to provide a very high level of emulsion stability.”
Improved service life and cleanliness
ITT Bornemann now has around 40 machines that use Blaser coolant, and more are to be added soon until the entire production facility uses Blaser products. ITT Bornemann states: “Switching to B-Cool 9665 brought a lot of advantages. Material compatibility, skin compatibility and odor have been significantly improved. Sump life has also increased immensely – instead of having to change the coolant four times a year, we now change it approximately every two years.” The machines are now much cleaner. Finally, coolant consumption has been halved due to extended service life and reduced top-up rates.
The high-tech pump system manufacturer adds: “In addition to the obvious advantages of the new coolant, we particularly appreciate the way we co-operate. Performance is regularly measured and documented on site, and we enjoy a constant, competent exchange of information. The Blaser laboratory in Switzerland is also very helpful in further optimizing processes.”
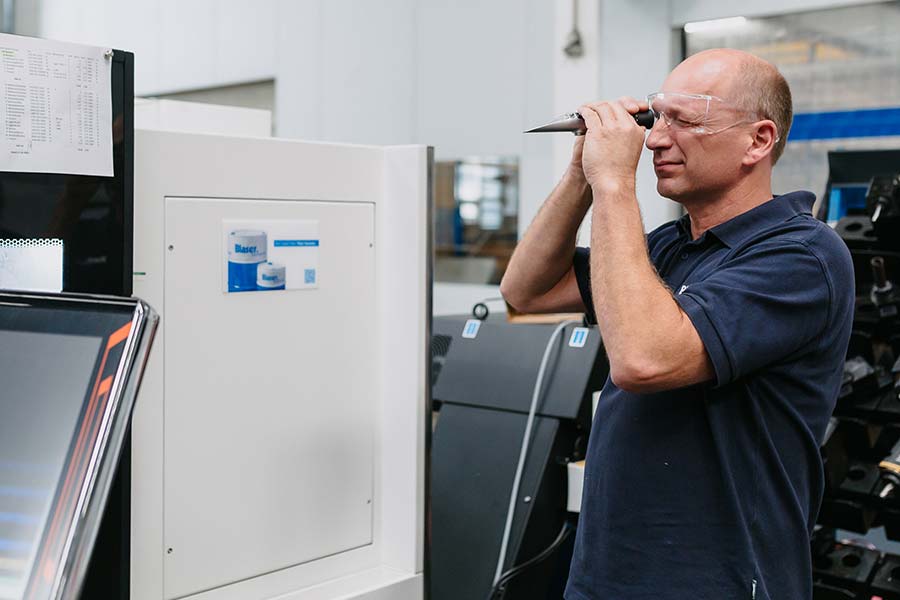
Application Engineer Carsten Liesegang, Blaser Swisslube, is responsible for on-site service at ITT Bornemann and carries out regular measurements in accordance with TRGS 611.
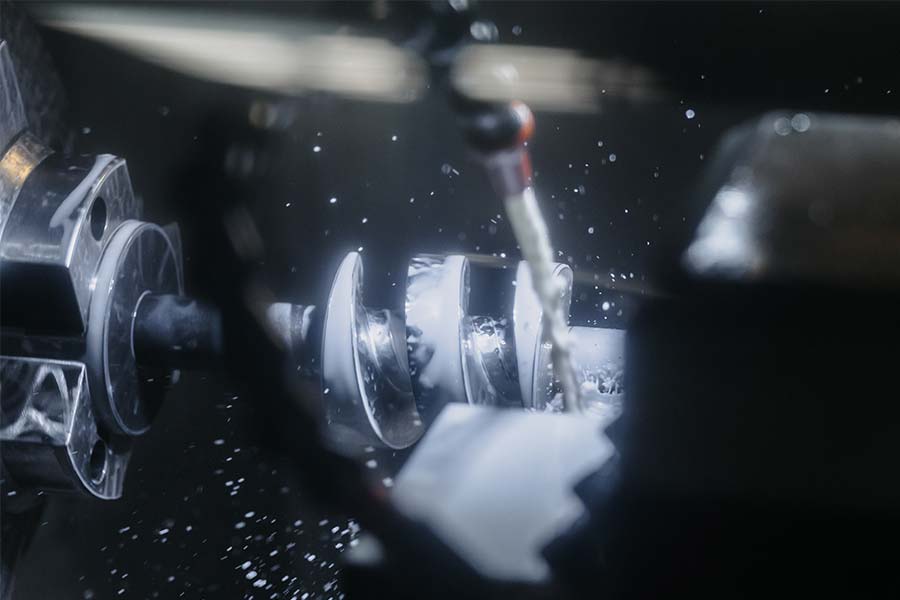
B-Cool 9665 features impressive cutting performance and excellent rinsing characteristics.
“We offer more than just a coolant. Through our advice and all-around service, as well as the precise adaptation of the coolant to the respective challenges faced, we offer a Liquid Tool that increases overall productivity,” emphasizes Joe Hollmann, Technical Sales Advisor at Blaser Swisslube. “Technical dialog with customers and regular monitoring of the metalworking fulid are key.”
The ITT Bornemann team sums up in conclusion: “In terms of biostability, productivity, human compatibility and versatility, Blaser B-Cool 9665 is the best coolant we have ever had. We are looking forward to further boosting productivity when we switch over our entire production to Blaser.”
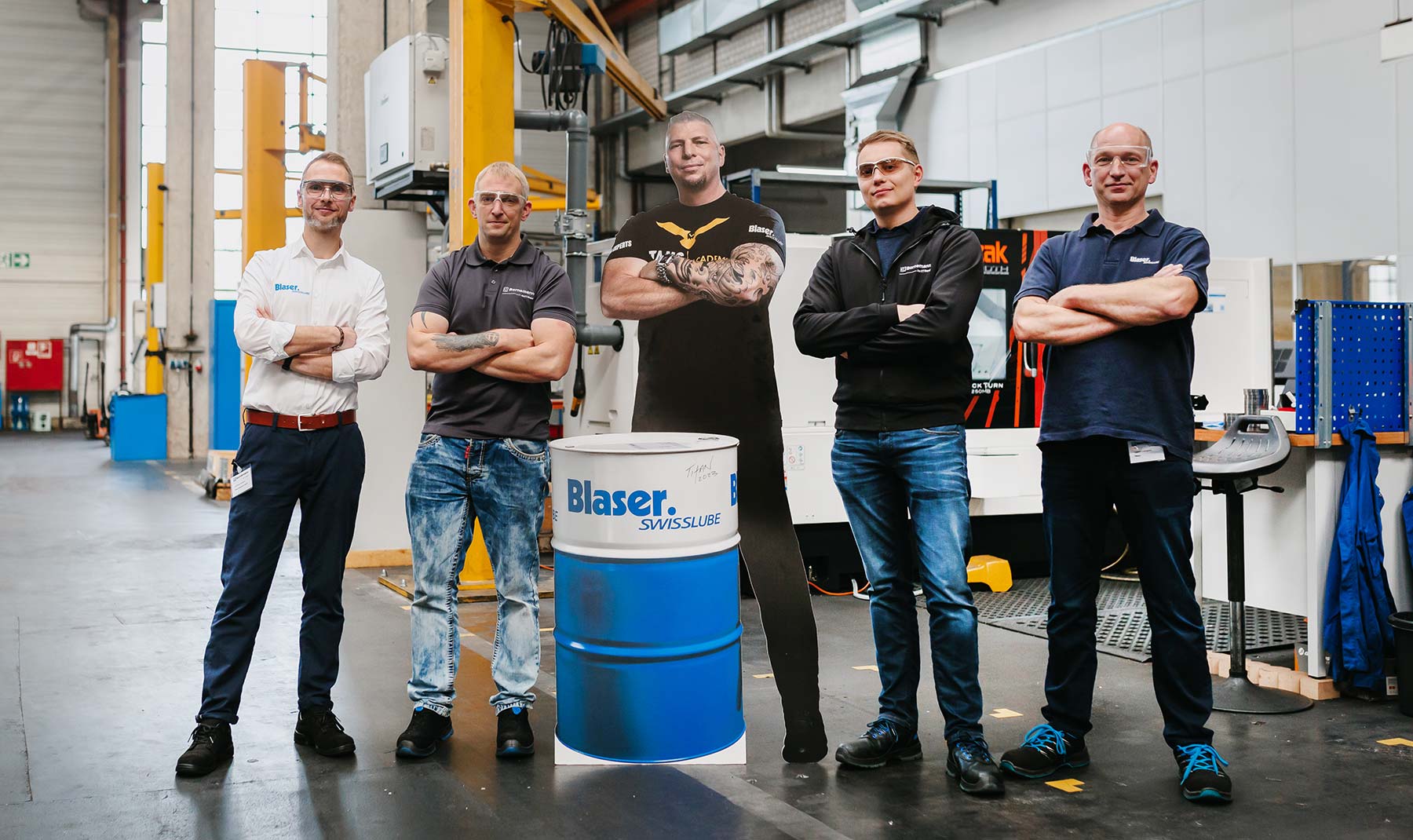
BOOM – strong collaboration.
Left to right in the photo: Joe Hollmann, Technical Sales Advisor at Blaser Swisslube; Oliver Sievert, CNC/CAM Programmer at ITT Bornemann; Philip David, Engineer at ITT Bornemann and Carsten Liesegang, Application Engineer at Blaser Swisslube.