New cutting oil for maximized workplace safety and productivity
© Intoolges The Catalan high precision manufacturer Joan Bonastre Group opened recently a new production plant in Barcelona. The modern building has the shape of a ship.
After the Catalan high precision manufacturer Joan Bonastre S.A. opened a new production plant, the technicians identified a number of problems in the workshop: Smoke development and a strong odor. Additionally, the tool life and the surface quality were worthy of improvement. Together with the metalworking fluid specialists of Blaser Swisslube, the right tool was found to solve all these problems: A change to the Blaser cutting oil Blasomill GT 15 maximized both the workplace safety and the productivity.
The Bonastre Group, based in Barcelona, consists of the Joan Bonastre S.A. and the Bonastre Biomed S.L. The family owned business has a long tradition dating back to 1958. The synergy between the manufacturing and engineering departments, the broad network of specialized suppliers and the more than 60 years of experience allowed Bonastre Group to establish itself as a leading manufacturer of all kinds of parts for medical devices and industrial products. The company is known as a benchmark for quality in advanced machining and high precision, offering added value and full service to its customers.
Bonastre Group works with and for their clients, in personalized and confidential way, complying with the requirements and standards required. The company is certified with UNE 166002 as well as with ISO 9001 and ISO 13485, and in 2021 ISO 14001. Just recently, the high-tech company inaugurated a new production plant.
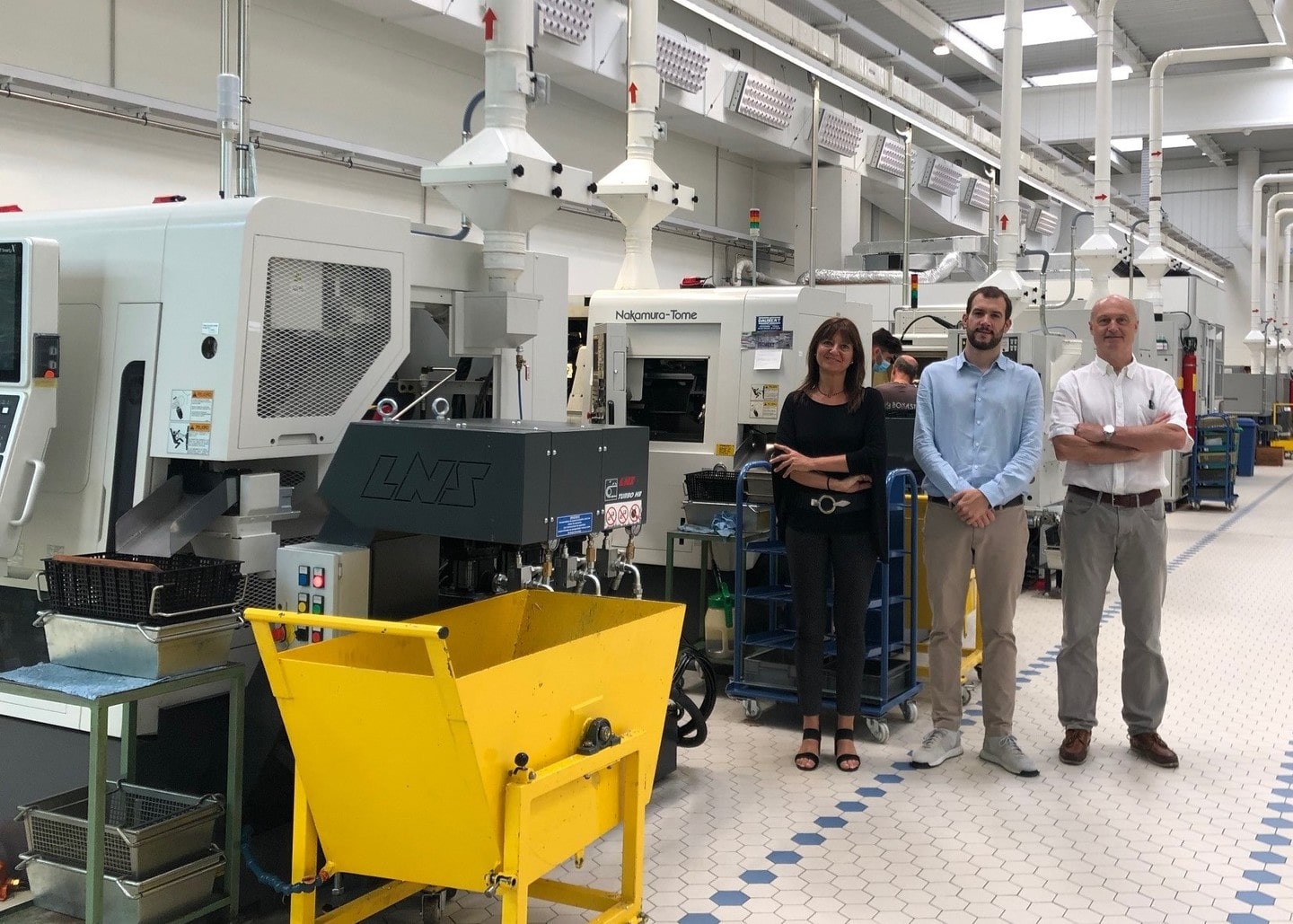
© Intoolges The Bonastre family in the new production hall, where industrial products are manufactured.
Already for several years prior to the opening of the new plant, Mr. Vicente Giner, CEO of Intoolges, the Spanish Blaser Swisslube business partner, has been in close contact with the Bonastre Group engineers, introducing the Blaser Swisslube product and the extensive concept of a Liquid Tool: When the metalworking fluid or cutting oil is tailored to the needs, processes, materials and surroundings, it can become a Liquid Tool and considerably improve the productivity and efficiency of the whole process.
A new solution for the new production plant
The production in the new plant started with neat oils from another manufacturer – but soon it became clear that a different solution was needed. Mr. Joan Jordi Bonastre, CEO of Bonastre Group, explains: “Now that the exclusive production plant with its new halls and offices was up and running, the productivity, quality and above all the odor and smoke development had to be improved.” The internal cooling for drills and mills was improvable. Furthermore, Bonastre Group could not achieve the best performance with high-pressure pumps.
Blasomill GT 15: low viscosity, high flash point
The production in the new plant started with neat oils from another manufacturer – but soon it became clear that a different solution was needed. Mr. Joan Jordi Bonastre, CEO of Bonastre Group, explains: “Now that the exclusive production plant with its new halls and offices was up and running, the productivity, quality and above all the odor and smoke development had to be improved.” The internal cooling for drills and mills was improvable. Furthermore, Bonastre Group could not achieve the best performance with high-pressure pumps.
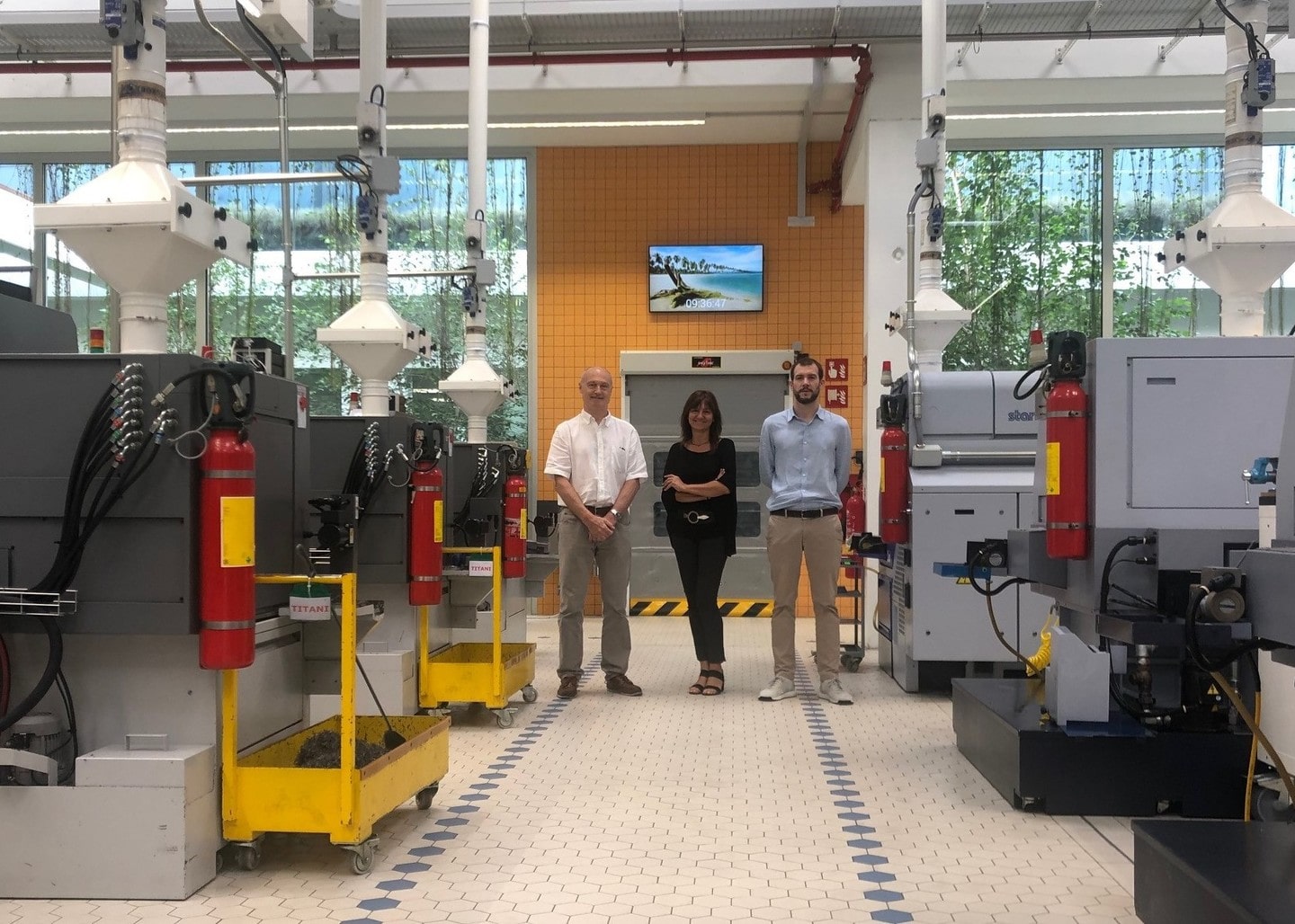
© Intoolges Medical division, where ten machines were selected for a test phase
Odor and smoke reduced significantly
In cooperation with the Joan Bonastre engineering team, ten machines from the medical division were selected for a test phase. And the results were very convincing: After only four weeks of testing, Blasomill GT 15 was filled in all 30 machines in the workshop. The Blaser cutting fluid was able to convince in all specified tests. Maybe most importantly, the environment for the workers was improved considerably: Odor and smoke problems disappeared. An isolated case with skin irritation was also eliminated.
Tool life increased by 20%
Due to the lower viscosity and the better lubrication behavior, the tool life was increased by up to 20%. Internally cooled tools were able to dissipate the heat better. Last but not least, the surface quality was improved thanks to the better lubrication properties.
“The new product Blasomill GT 15 not only optimized the machining quality and productivity, it was also very well received by our machining operators in terms of cleanliness and clarity. The workpieces can now be seen during machining, making process monitoring and earlier intervention possible,” concludes a pleased Mr. Joan Jordi Bonastre.
Bonastre Group, Intoolges and Blaser Swisslube aim to continue to cooperate to increase the productivity as well as the health, safety and comfort of employees.