Minimum quantity lubrication (MQL) – ready for Industry 4.0
Oil quantity, volume flow and pressure of the MQL aerosol can be directly taken into account in the digital process chain. This offers a clear advantage in comparison to conventional metalworking fluids.
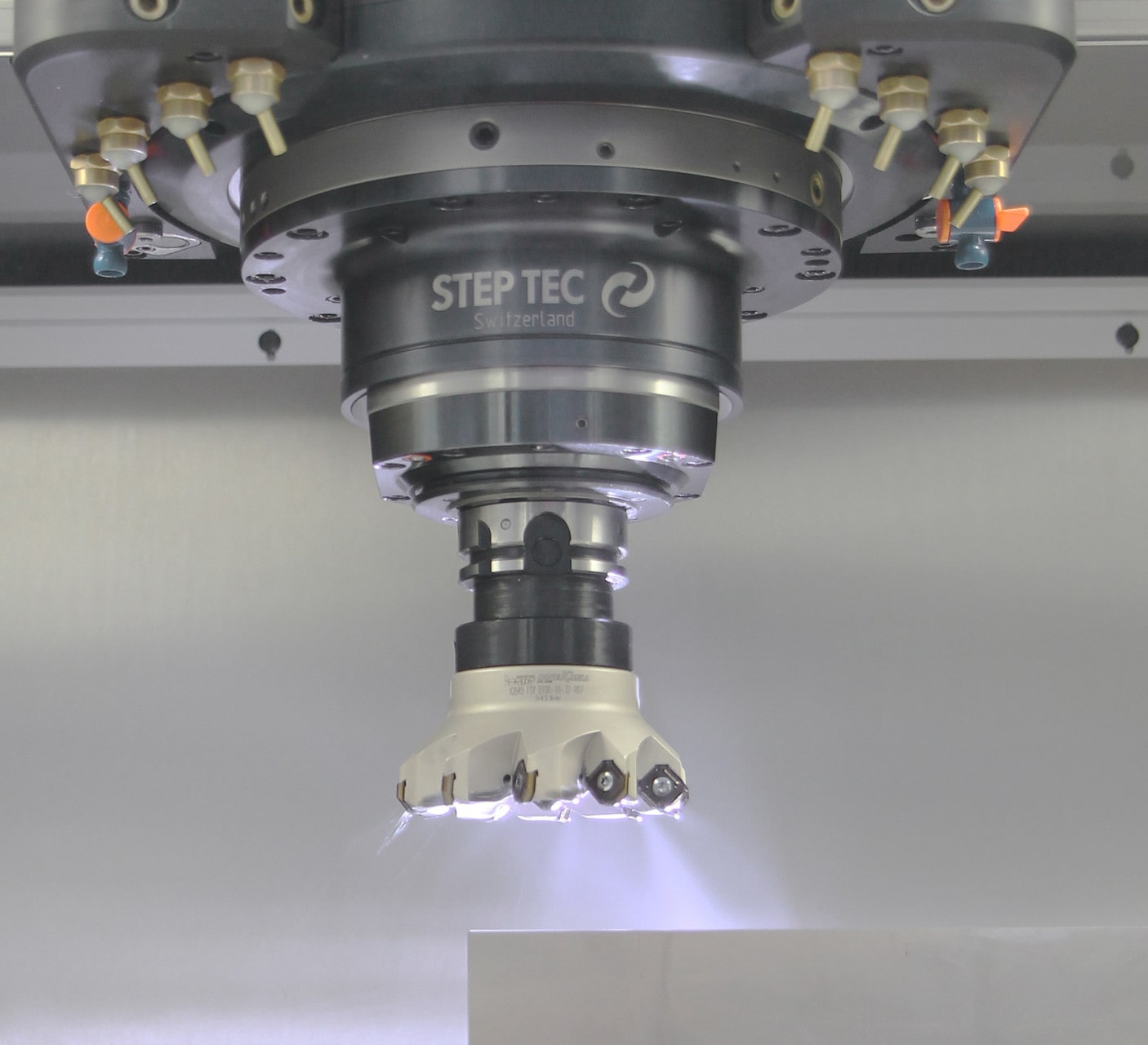
Figure 1: Good spraying behavior
Effective delivery of metalworking fluids
Metalworking fluids, minimum quantity lubrication and cryogenic components are complex issues. Regardless of the method, the basic objectives of the cutting industry are high process reliability and high productivity. In addition to the economic ideas, ecological aspects are playing an increasingly important role. When things work out well, they can, in turn, also offer potential savings in energy and other resources.
All metalworking fluid-related lubrication methods, including MQL, have a common characteristic: continuous targeted feeding of the metalworking fluid into the cutting zone. The metalworking fluid must be delivered accurately onto the rake and flank face of the cutting tool. This can best be achieved by means of an internal metalworking fluid supply.
Processes and advantages with Minimum Quantity Lubrication (MQL)
The MQL process creates an aerosol comprised of an oil-air mixture. This mixture forms a protective film, which reduces the friction and directly prevents the tool’s wear. Cooling of the cutting tool is achieved / controlled by means of forced convection via compressed air, wet surfaces and evaporation enthalpy.
Processes such as high-speed cutting (HSC) or high-feed cutting (HFC) are fundamental prerequisites for cutting successfully with MQL. In this case, an MQL-optimized cutting process requires smaller, constant wrap angles in order to reduce the total heat input into the tool.
In recent years, there has been a significant development both in the field of MQL devices, delivery systems and the cutting tools themselves. Compared to wet machining, MQL is a more flexible application, since smaller amounts of fluid are fed. However, due to this reduction of fluid, it is imperative to pay close attention to the continuous and targeted feeding of the cutting tool with the MQL aerosol. The low energy consumption, the cleanliness of the parts and chips, as well as good material compatibility are further advantages of this method.
MQL and Industry 4.0
The integration of MQL and modern MQL systems in the digital process chain can be realized more easily and quickly than with conventional metalworking fluids. The regular measurement of the various parameters such as concentration, pH value etc. becomes completely unnecessary. As MQL normally means oil, detecting impurities, particle sizes etc. poses hardly any problems. In the course of MQL machining, the amount of the oil fed and the compressed air is recorded (volume flow and pressure) in modern MQL systems. This data can be linked directly to the product and process data in the digital process chain. Thus at the desired time, all essential process variables from the cutting tool to the machine tool, feed, speed as well as the lubricant supply can all be monitored.
Considerations such as compressed air consumption, associated power consumption and losses can be adjusted and estimated according to Dr. Ivan Iovkov (cf. Iovkov, 2016). Aerosol quality and oil fraction measurement during nozzle discharge are more complex tasks, which can, however, be solved by a unique subjective adjustment by the machine operator for the respective tool.
The following example of high-feed cutting of stainless steel (Inox) shows the potential of an MQL strategy exceptionally well.
Successful MQL attempt at Blaser Swisslube Technology Center
Until recently, the milling process on 1.4307 had been primarily machined dry. The aim of the project was to optimize the process with MQL and to achieve added value. The first step was to compare various Fraisa milling tools and MQL products manufactured by Blaser Swisslube. Subsequently, different processes were evaluated with the best tool size and the best MQL oil. An overall view of the entire process is essential for optimal MQL machining. This includes the MQL device itself, the aerosol as well as preparation and delivery. The tooling must be designed from the start for MQL delivery. Only when a constant and consistent aerosol with good spray behavior (Figure 1) is generated at the tool discharge nozzle can improvements be successfully implemented.
Result: longer tool life and increased productivity
During the test, the MQL product Vascomill MMS FA2 showed an impressive performance and helped to increase tool life by 243%, at the same time increasing the feed rate and the cutting speed. The latter increased from 130 m/min to 390 m/min. This ensured a total productivity increase of more than 70%. Furthermore, the optimum MQL strategy prevented the built-up edge on the cutting edge (Figure 2).

Figure 2: MQL prevents built-up edges
Increase of the tool lives by a factor of 12
Materials such as aluminum alloys, conventional steels and stainless steels offer a very high potential for MQL machining, since the heat can dissipate easily through the chip. In the field of turbocharger production, the tool life increased by a factor of up to 12 in comparison to conventional metalworking fluids and dry machining. This is due to the fact that the brittle and hard indexable inserts react to the change in temperature during coolant machining. Furthermore, conventional coolant machining also requires ductile inserts and coatings. This is the advantage of MQL machining. (Figure 3)
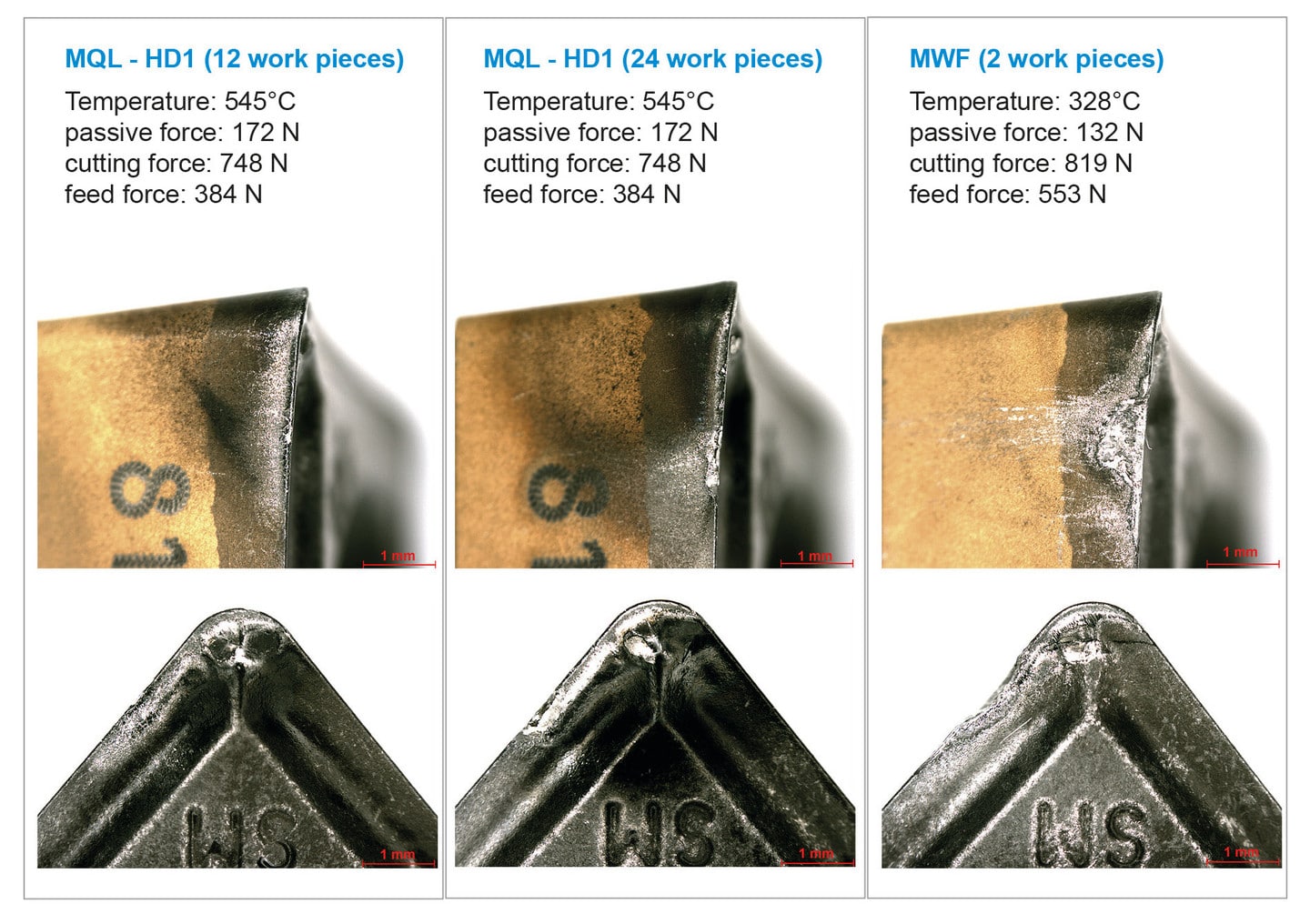
Figure 3: MQL (minimum quantity lubrication) machining in the case of 12 or 24 workpieces vs. wet machining (metalworking fluids) for the turning of 1.4837 lowNi
Titanium machining with MQL
Materials which are difficult to machine, such as titanium and inconel, are a major challenge for MQL applications. Excellent tool life and cutting speeds can be achieved in the area of thread rolling and the cutting of titanium. In milling and drilling however, the corresponding tools and machining strategies have not yet been fully determined. In this area, some questions remain unanswered. Further research and a deeper understanding of the machining processes, as well as their further development are necessary.
References:
Iovkov, Ivan (2016): Technologische Analyse des Tieflochbohrens mit Minimalmengenschmierung und simulationsbasierte Kompensation des Mittenverlaufs, ISF TU-Dortmund