
2. Prozessauswahl: Bei der Prozessauswahl ist darauf zu achten, dass ein stabiler Prozess zum Vergleich ausgewählt wird. Andernfalls kann die Prozessstreuung die Beurteilung der Kühlschmierstoffe stark verfälschen.
3. Los splitten: Bestenfalls wird ein grösseres Produktionslos gesplittet (Material- sowie Werkzeugchargen gleichmässig auf die Kühlschmierstoffe aufteilen). So kann bei den zu vergleichenden Kühlschmierstoffen eine möglichst gleiche Ausgangslage geschaffen werden.
4. Beurteilungskriterium wählen: Nun kann verglichen werden, mit welchem Kühlschmierstoff die Werkzeuge länger einsatzfähig sind. Hierzu ist vorgängig ein klares Kriterium zu definieren, welches von der vorhandenen Infrastruktur abhängt. Entweder werden beispielsweise die gleiche Anzahl Teile gefertigt und die Werkzeuge anschliessend genau vermessen und verglichen. Oder es wird ein anderes eindeutiges Wechselkriterium festgelegt (zum Beispiel via Lastüberwachung eine Grenze definieren) und im Anschluss wird die gefertigte Stückzahl verglichen.
5. Repetieren/Wiederholen: Bei Versuchen gilt immer die Devise: ein Test ist kein Test. Wir fahren hierzu bei unseren Prozessen immer mindestens drei Tests um die Streuung der Resultate abzuschätzen. In den Metallbearbeitungsbetrieben ist die Anzahl Versuche Losgrössen abhängig. Es gilt: je mehr Werkzeuge ans Standzeitende gefahren werden umso besser ist das Resultat statistisch abgestützt.
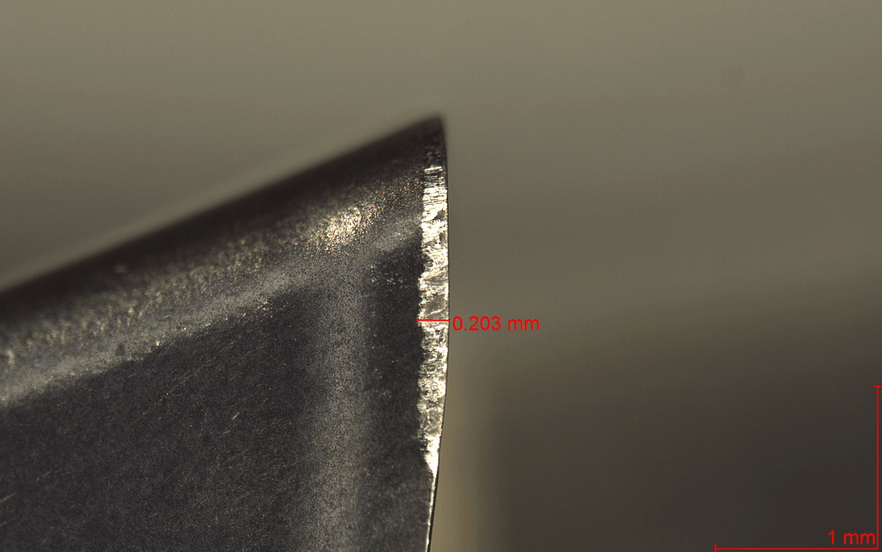
Bei unseren genau definierten Tests im Technologiecenter werden die Werkzeuge nach festgelegten Intervallen auf unseren Mikroskopen genau betrachtet und der Freiflächenverschleiss exakt bestimmt. In den meisten Fällen liegt die Verschleissgrenze bei 0.2 bis 0.3 mm. Dies entspricht ungefähr drei bis vier nebeneinander gelegten Haaren. Dies ist vergleichsweise wenig, jedoch nehmen danach die spontanen und unregelmässigen Ausbrüche und Abplatzungen stark zu. In der Industrie bedeutet dies eine schlechte Prozesssicherheit und führt zu Ausschuss.
