The metalworking fluid turbo for the automotive industry
Everyone in the automotive industry is talking about emission values and downsizing of combustion engines right now. In order to accelerate basic research in the field of turbocharger manufacturing, Blaser Swisslube, in collaboration with their partners, have carried out extensive tests at the company’s own Technology Center. The automotive suppliers and sub-suppliers are extremely interested in the findings, especially the savings potential.
The diesel scandal surrounding the manipulated emission values is still lingering in people’s minds. The CO2 requirements in Europe are ambitious. By 2020, output is to be limited to 95g CO2/km. Downsizing is a hot topic for the automotive suppliers. Turbocharger boosts help whip the engines into shape with low displacement. When it comes to passenger vehicles, the turbocharger production numbers are expected to increase to 60 million units per year by 2020. This is an increase of appr. 27 percent, despite growing electromobility.
But the production of turbochargers is very complex. Stable and reliable processes as well as high productivity are crucial. Tests carried out at Blaser Swisslube’s own Technology Center in Switzerland have clearly demonstrated what can be achieved with carefully planned processes and the right metalworking fluid.
Tool life increased from 1,200 to 2,000 drills
In 2013, Blaser began to carry out tests together with a leading tool manufacturer in the field of turbine housing machining. This involved machining heat resisting cast steel (1.4849, 1.4848 as well as 1.4837). The aim of the tests was to find the ideal tool/metalworking fluid combination, thus creating added value for the customer. The benchmark for the testing was drilling and face milling using original components and test components. The tools and the metalworking fluid strategy were carefully planned for each machining process. Thanks to Blaser’s Liquid Tool, the tool life of 1,200 drills was increased to over 2,000 drills. When it came to face milling, the tool life was increased to up to 25 percent for rough cutting and appr. 45 percent for finishing.
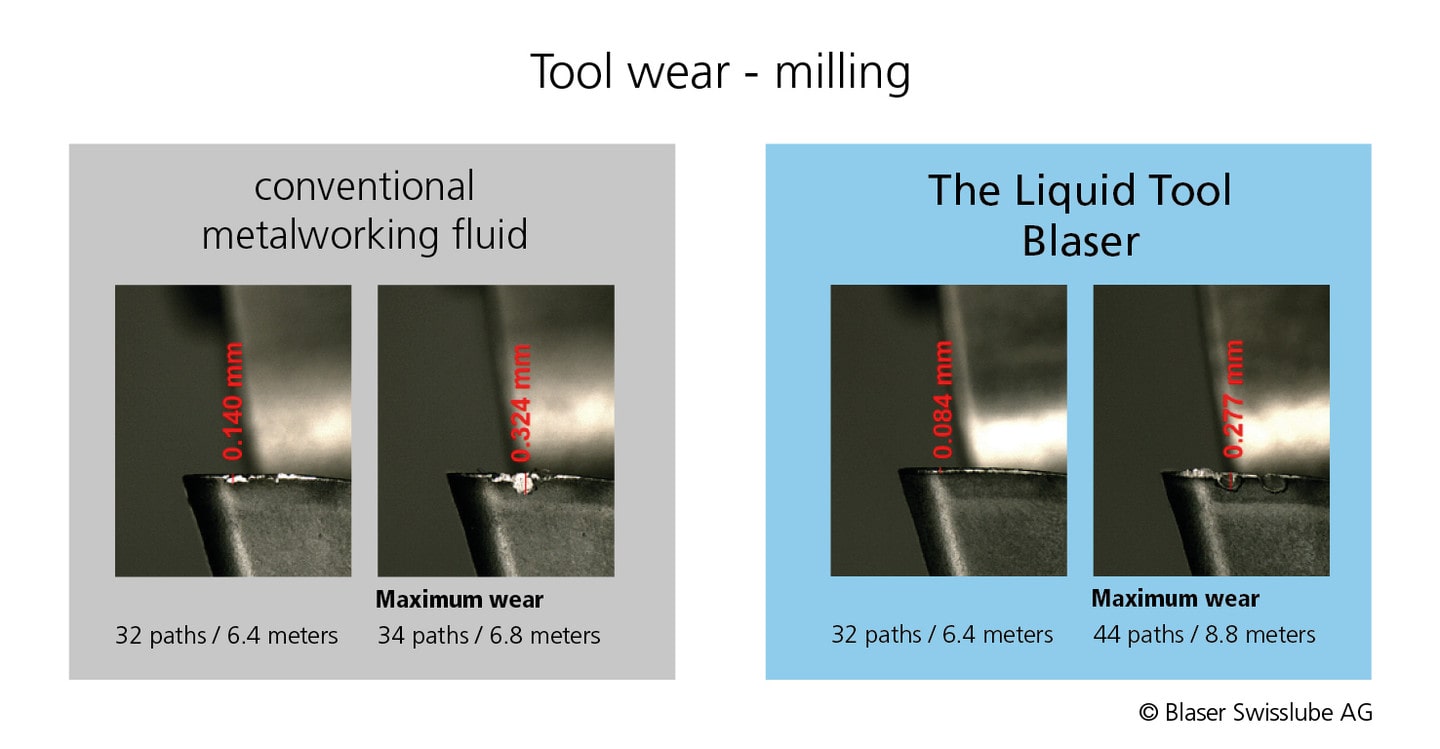
Higher tool life thanks to Blaser’s Liquid Tool
Basic research
In close collaboration with a leading OEM in the field of turbocharger production, a further project was launched in 2017. The aim of that basic research project was to answer the following question: What is the ideal metalworking fluid strategy for machining turbine housings? Numerous tests were carried out at Blaser’s Technology Center, as well as in the premises of leading machine tool manufacturers. The focus was on process security, cost reduction and process stability. Special attention was paid to the interaction of the cutting materials, metalworking fluid strategies and machining materials.
Significant cycle time and tool cost reduction
With the help of the findings, one automotive sub-supplier from India was able to reduce their cycle times by an incredible 5 seconds without sacrificing the process security. But that’s not everything. One large European car sub-supplier was able to save a total of 20 percent of tool costs for drilling, V-band roughing (using bell tools) and milling in the course of a three-shift operation. The metalworking fluid’s sump life significantly increased, too (by over 50 percent) thanks to the Blaser’s new metalworking fluid solution.
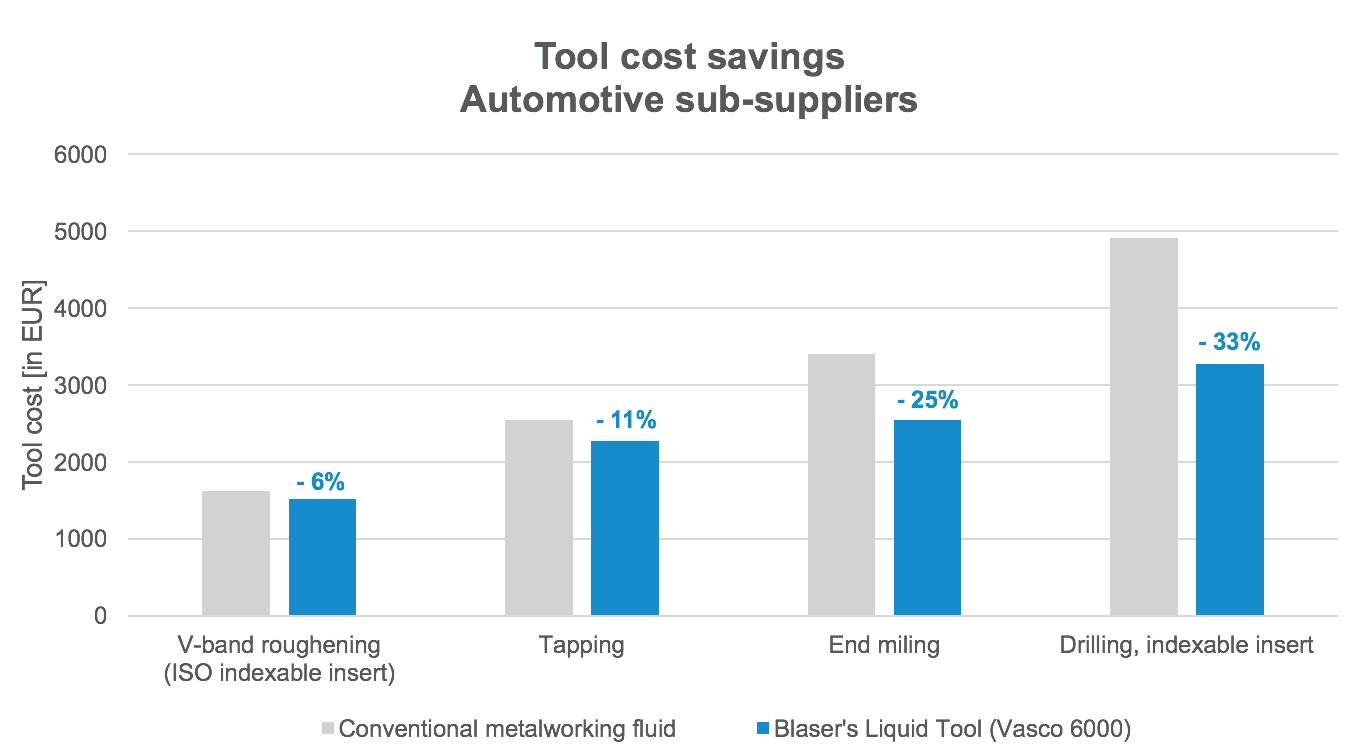
Reduced tool costs for a European car sub-supplier
The Liquid Tool by Blaser Swisslube
This project made quite clear that factors such as productivity, economic efficiency and machining quality strongly depend on the choice and quality of the metalworking fluid and know-how of the machining specialists. In addition to the coolant, it’s Blaser’s expert knowledge in the areas of sales, research and development, technology and customer service that solidify their status as an excellent partner. This professional competence transforms a metalworking fluid into a Liquid Tool, a solution that is tailored to the partner’s specific needs.
Downloads
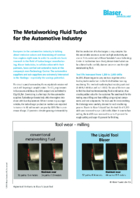