Sustainability is the primary objective
Biral Headquarters in Münsingen, Switzerland
The situation facing Biral AG, the leading Swiss pump manufacturer, in its production hall was anything but optimal, with an unstable emulsion and unsatisfactory coolant service life the least of the company’s problems. The greatest concern was the skin irritation suffered by three employees. Analysing the various manufacturing processes and switching to the optimal Blaser metalworking fluid transformed production into a sustainable process. Even more importantly, skin problems are now a thing of the past.
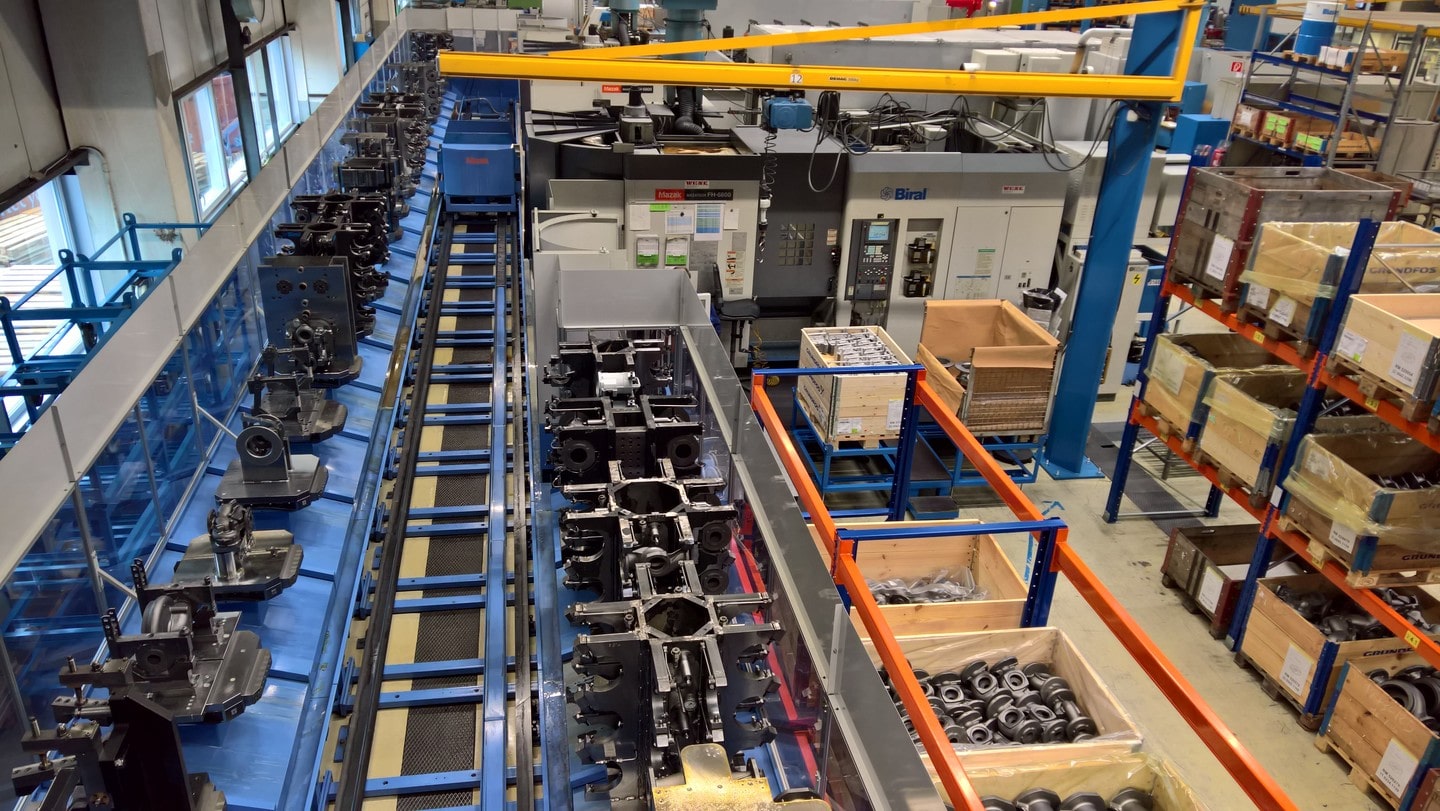
View of the shopfloor
Biral AG, headquartered in Münsingen, was founded in 1919. From the outset, the company built up its reputation as a manufacturer of state-of-the-art pumps for building services, municipal applications and industry. The 165 employees are committed to the goal of producing the best pumps around. The manufacturing process involves a comprehensive mate-rials mix. The pump housings are made from grey cast iron. Bronze is machined for various components, while aluminium and steel are also produced.
Grey cast iron machining accounts for the majority (around 80%) of the production processes at Biral AG. Aluminium and steel make up around 15%, and there is one machine for working bronze. “It is not easy to handle such a diverse mixture of materials,” explains Martin Haas, application engineer at Blaser Swisslube, Switzerland.
It was no surprise, therefore, that the situation in the pump manufacturer’s production hall was anything but optimal. The service life of the coolant being used was unsatisfactory, and the emulsion had to be adjusted at regular intervals by add-ing additives. Three employees complained of skin irritation caused by the unstable metalworking fluid. Faced with these problems, Biral staff were reminded of a metalworking fluid seminar at Blaser Swisslube. Biral contacted Blaser in search of a sustainable solution.
Liquid Tool
Blaser’s experts scrutinised all aspects of the situation in the production hall. “In combination with materials, tools and processes, the right metalworking fluid becomes a Liquid Tool. Our objective was to get the skin irritation under control and sustainably improve Biral’s processes by choosing the right product,” says Haas. The analysis focused in particular on the materials mix. We identified green discolouration, often found when working bronze. We therefore had to find a product that was also appropriate for this application.
Based on experience with other cases, the Blaser application engineer recommended switching to Blasocut BC 935 Kombi. The water-miscible, mineral oil-based metalworking fluid is bactericide and boron-free, high-performing, robust and universal. “Blasocut BC 935 Kombi offers excellent properties for machining cast iron, but can also be used for a broad materials mix. And first and foremost, this coolant is not harmful to humans or the environment,” explains Haas.
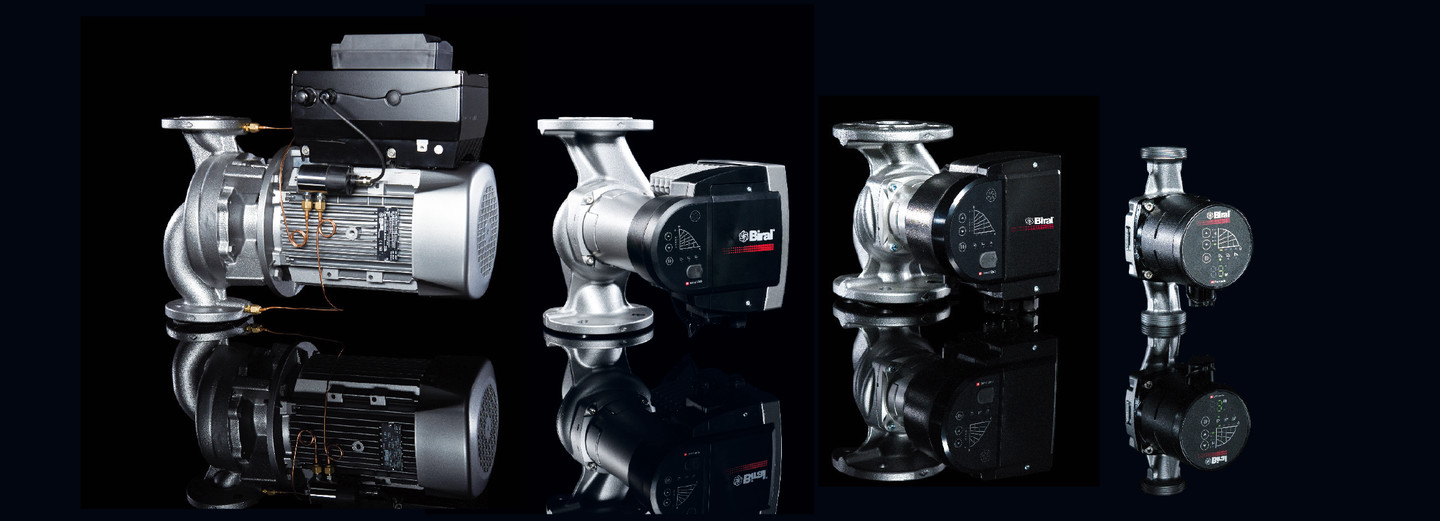
Produced pumps by Biral
The results after the switch speak for themselves: The new metalworking fluid solution has a service life of a year, and there is no longer any need for expensive control additives. “This was also achieved with the previous product, but only through large-scale use of bactericides and fungicides, which were not included in the cost breakdown,” reports application engineer Martin Haas.
An investment that pays off. The increased tool life resulted in overall cost savings of ₩ 392,000 and in addition saved time of tool regrinding. Even though the coolant costs of Vascomill CSF 35 are higher than for the previous product. The expected leverage effect has been confirmed.
Yoon Dong-seop is now convinced that the right coolant solution has a positive effect on the entire process and the overall costs. Yoon Dong-seop said, “We’ve learned how important it is to use a good coolant in the entire process.” Going forward, JinMyeong PowerTech and Blaser Swisslube Korea will work in close collaboration to ensure a win-win business relationship moving forward.
A sustainable process
“Blaser Swisslube helped us transform an intermittently functioning process into a wholly sustainable one,” says Biral production manager Michael Schütz, who is very satisfied with the outcome. “The operating costs have increased slightly due to the higher concentration of metalworking fluid, but this is an investment that pays for itself and has ensured that we no longer have any problems whatsoever with skin irritation.” Biral AG and Blaser Swisslube plan to work together to further optimise production processes.
Blasocut Bio-Concept
Blasocut BC 935 Kombi is a coolant out of the Blasocut line. The Blasocut products have an excellent human and environ-mental compatibility. The technology has been able to cont-ribute to the robust process of machining, high productivity, and better machining quality. In today‘s manufacturing world, it has become a global requirement for all manufacturing in-dustries to contribute towards a Green Planet. There is a high level of awareness about the ill effects brought in by many factors of industrialization. Sustainable technologies like the Blaser Swisslube Bio-Concept work in perfect harmony with nature. With the Blasocut Bio-Concept, emulsions need no tank side addition of bactericides.
They stay inherently biologically stable. These emulsions have a unique way of maintaining the long-term bio-stability of metalworking fluid emulsions. The Bio-Concept uses an age-old law of nature whereby bacteria normally colonize aqueous media immediately. To keep the emulsions stable, deliberately foster this by creating ideal conditions for harm-less primary bacteria. These bacteria, also present in drinking water, build up a naturally stable biotope where undesirable bacteria have no chance of propagating.
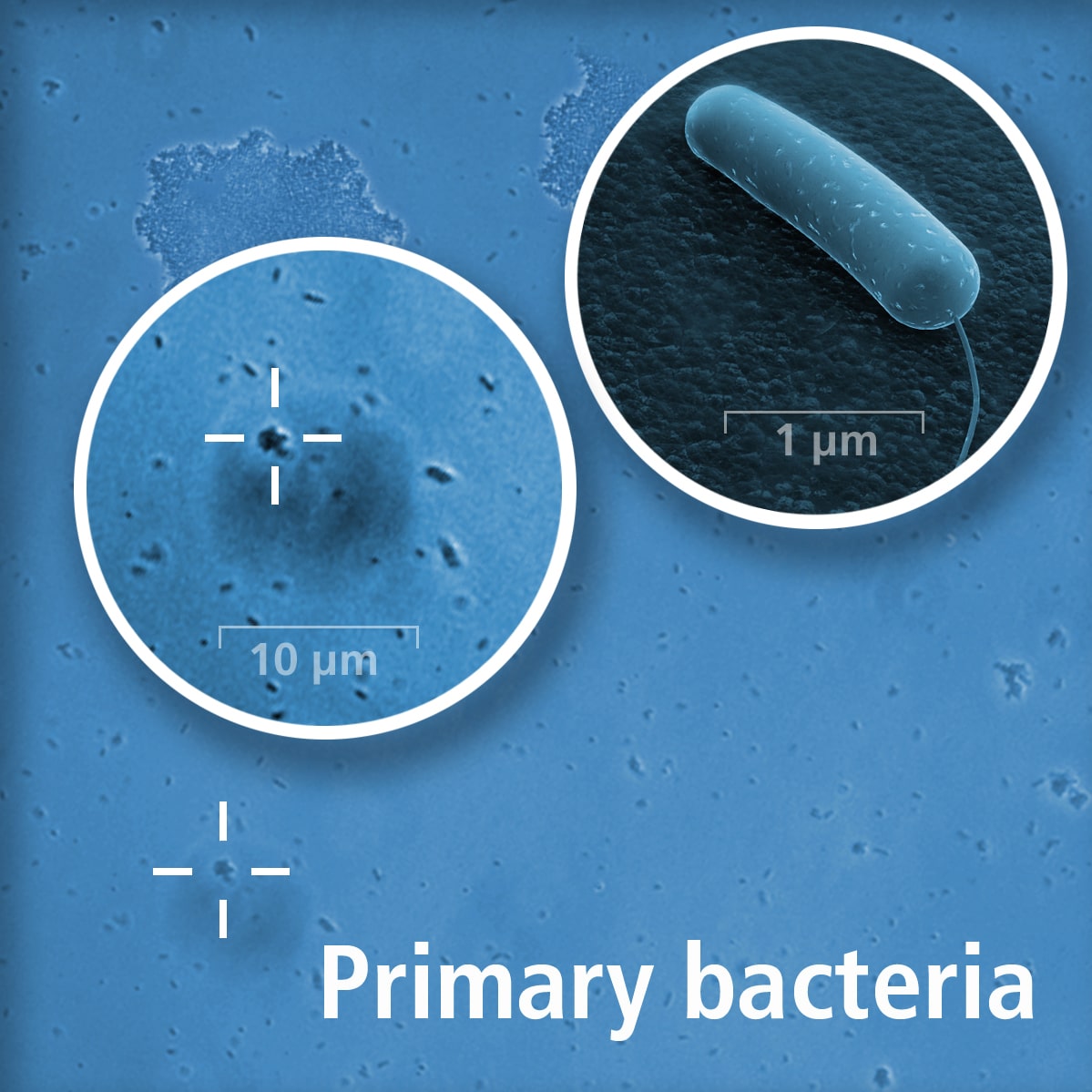