Research on the processing of turbine blades with minimum quantity lubrication
Demo blades at Liechti Engineering on a Turbomill 1400i (turnaround time: 63min). The mass of the blank amount to: 150x70x480mm.
Blaser Swisslube has carried out an extensive analysis of the milling of steel turbine blades in collaboration with GF Machining Solutions AG – Liechti Engineering and Walter AG. Conclusion: Minimum quantity lubrication (MQL) makes it possible to optimise the process and offers a savings potential when it comes to tool costs.
The collaborative effort began about 1.5 years ago. Liechti Engineering initiated the project, intending to optimize the processing of turbine blades with the support of Blaser Swisslube and Walter. The blades, made of high-alloyed heat-resistant steel, are first roughened, and then pre- finished before a final finishing. The key processing phase in particular (meaning: the longest cycle time, and thus the highest production costs) was carefully examined throughout the course of the project.
Blaser Swisslube’s Technology Centre
During the initial tests at Blaser Swisslube’s in-house technology centre at the headquarters in Hasle-Rüegsau, X20 chrome steel blocks were milled using a GF Mikron HPM 800U – both rough-ing and finishing. The processing was carried out using a metalworking fluid, MQL, as well as dry and with pure compressed air cooling, and subsequently compared. Various cutting parameters were used. The MQL processing demonstrated its merits when it came to reduced flank wear during finishing, and the surface finish was very good as well. It therefore proved to be the ideal choice for this process.
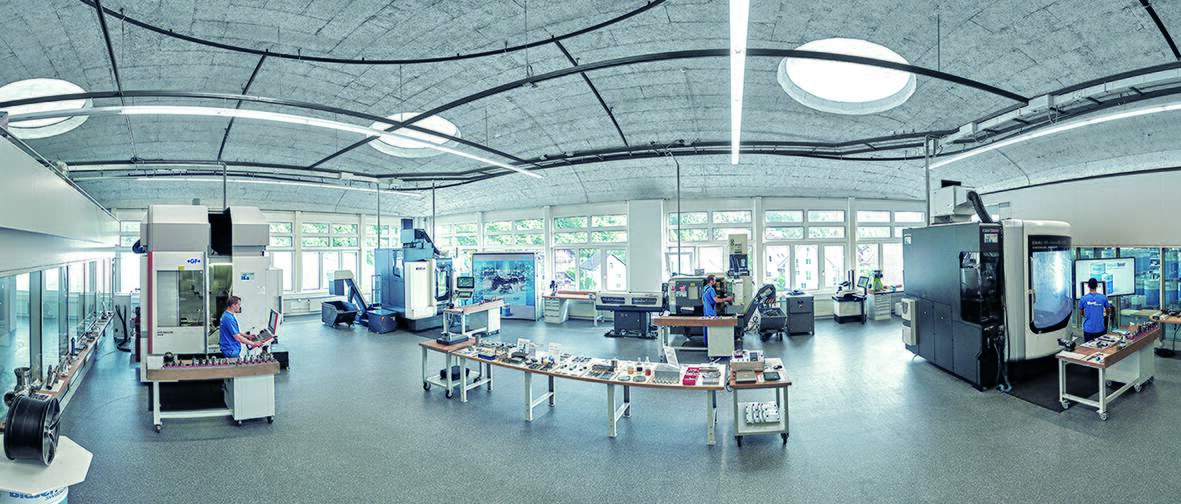
Technology Center and Competence Center of Blaser Swisslube in Hasle-Rüegsau
Research results obtained by Liechti Engineering
Further tests were then carried out at Liechti Engineering in Langnau. Blades were machined using a Turbomill 1400i. The results obtained match the findings made at Blaser’s technology centre. Apart from X20 chrome steel, Liechti Engineering also processed hard-to-machine X2 chrome steel in order to put the MQL process under scrutiny. Conclusion: Thanks to the MQL processing, the wear on the cutting edge is reduced and the tools have a longer life. This offers a savings potential with regards to the tool costs. Test showed that when finishing with MQL, tool wear can be reduced by a factor of up to 5 compared to metalworking fluid
Result of the collaboration
“MQL processing is the perfect choice for the tested machining process,” explains Simon Sakica, Blaser Swisslube’s Process Engineering Manager. “When roughening, this process involves working with air in order to keep the thermal shock to a minimum. When it comes to finishing, the MQL is the best possible solution. However, you have to ensure that the spray pattern is right. As no tanks are necessary for MQL processing, one also saves space in the factory workshop. However, you need to avoid any deposits of chip residues in the machine,” he concludes. This is something that requires further clarification.
According to the findings of Liechti Engineering and Walter, all cooling methods have their advantages and disadvantages. “In the best possible scenario, a machine can function both with a metalworking fluid and with MQL. One can use the right process for each session,” Andreas Finger from Liechti Engineering concludes.
This means that the project responsibles of Liechti Engineering, Walter and Blaser Swisslube will continue to be busy with the findings from the project.
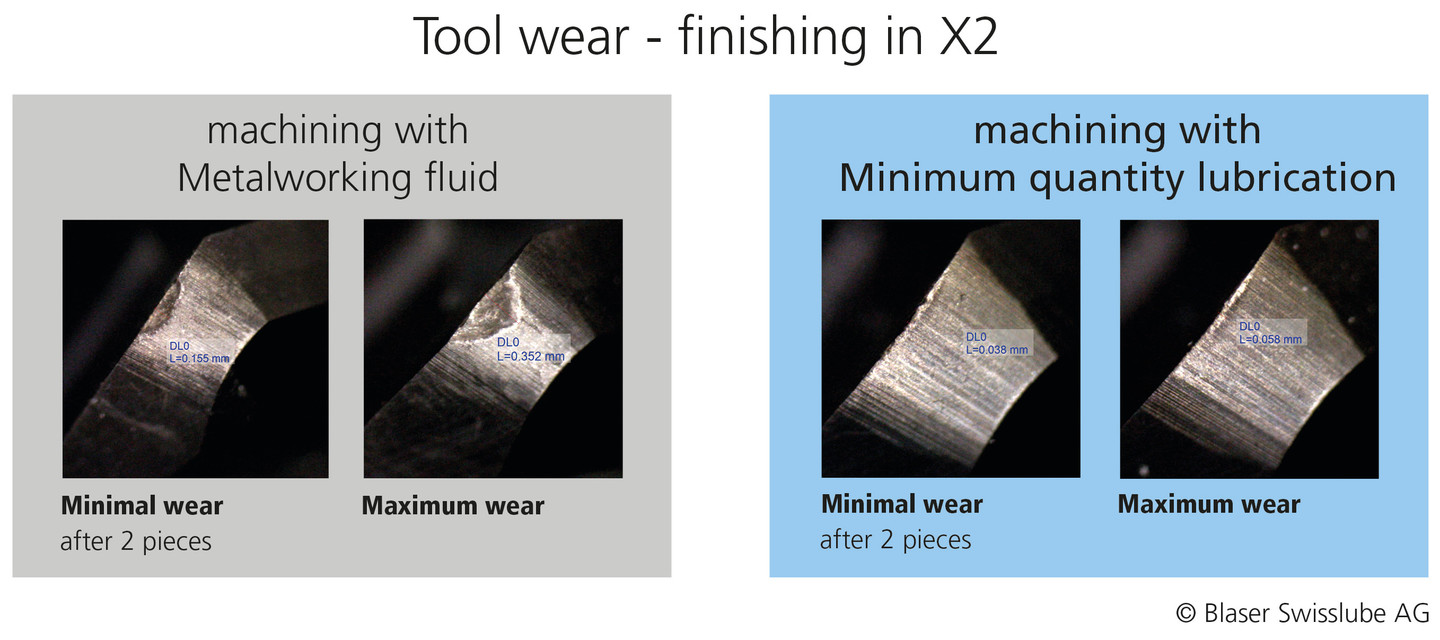
Comparison MQL vs. coolant machining with flank wear, tool: SC end mill ø19/R1, z=15
Blaser Swisslube’s Liquid Tool
The factors of productivity, economic efficiency and machining quality depend to a high extent on the choice and quality of the coolant used and the expertise of machining specialists. Thanks to professional expertise, a coolant becomes a Liquid Tool, a solution that is precisely customised to the requirements of the partner.
Liechti Engineering
Liechti Engineering is the worldwide leader for 5-axis profile machining solutions in the turbine industry for the aerospace and electricity production sector. These are the markets where Liechti Engineering has a reputation as an expert for turnkey solutions, including special machines, software, process technology, tools for flow profiles. Liechti Engineering’s milling machines reduce the processing times by over 30 percent thanks to their specific profile machining technology and the special CAD/CAM software. This high performance is due to the company’s engineering competence and the expertise in the field of 5-axis and highly dynamic machining of titanium, Inconel, Nimonic, titanium aluminide and high-alloyed steels.
GF Machining Solutions AG
Liechti Engineering
Kanalweg 4
3550 Langnau
www.gfms.com
Walter AG
Walter is one of the world’s leading companies in the field of metal working. The machining specialist offers an extensive range of precision tools for milling, turning, drilling and threading. Together with its customers, the company develops customised solutions for a complete machining of components in the fields of general machine construction, aerospace, car and energy industry.
Walter (Switzerland) AG
Hunnenweg 2
4501 Solothurn