Hizima Seiki, whose main factory is located in Nanto City, Toyama Prefecture, is engaged in the design, manufacture, and maintenance of plastic injection molds. Since its establishment more than 70 years ago, the company has been manufacturing molds mainly for round products and has accumulated a unique technological know-how. Hizima Seiki specializes in multiple-cavity cap molds for products in the pharmaceutical industry, medical devices, and food. The company is constantly striving to improve the three levels of its operations: high-specification machines, operators who are proficient in using the machines, and the technical skills of the mold finishing craftsmen. The innovative company’s strength lies in the thorough dimensional control and fast delivery speed achieved through integrated production at its own factory.
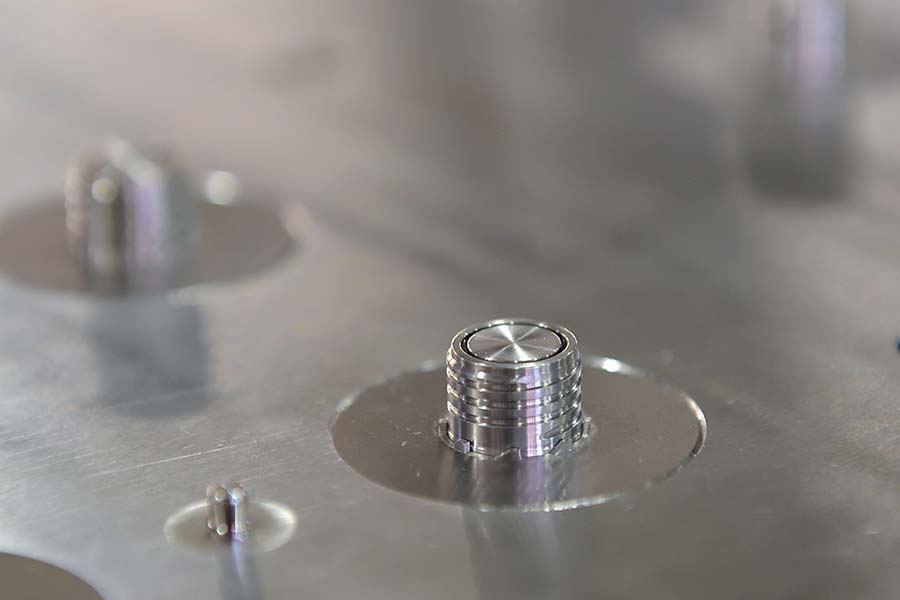
When Mr. Kawai shared the issues with Mr. Naohiro Shimaura, a Blaser Swisslube sales representative, he was recommended Synergy 735, which has a very low odor and minimal skin impact, and Vascomill 10, which has excellent lubricity and is gentler on the skin than mineral oil. Since the switch was made three years ago, the coolant has not caused hand irritation and odor. Synergy 735 was also beneficial in that it is clear and unobtrusive, making it easier to clean the machines.
The improvement in the factory environment was made possible in large part by the cooperation of Mr. Shimaura. The study sessions held during the introduction of the system enabled a deeper understanding of the causes that lead to spoilage and enabled the company to manage the coolant more efficiently. During his in-depth monthly monitoring, Mr. Shimaura checked the condition of the cutting fluid one machine at a time. His advice on how to manage each machine has led to considerable improvements in the factory environment.
Currently, metalworking fluids from Blaser Swisslube are used on ten machines. Because of their high effectiveness, 90% of the machines that are suitable have already switched to Blaser Swisslube products.
Hizima Seiki plans to continue using the products in the future. “Everyone in the factory appreciates the quality of the Blaser coolants as the putrid smell that used to pervade the entire factory has been eliminated”, says Mr. Kawai.
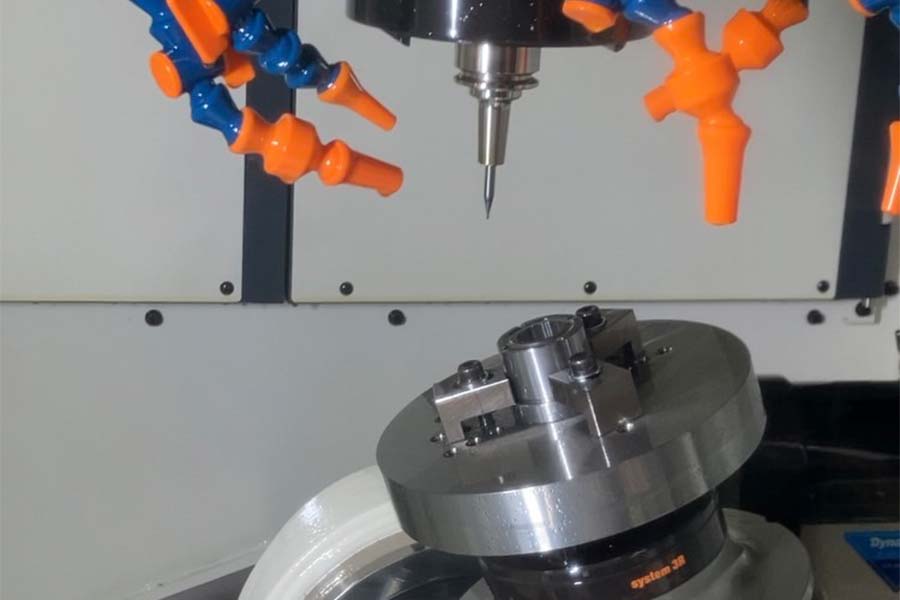